Advertisement
Advertisement
Protecting Against Marine Corrosion
How do I avoid corrosion when my boat moves regularly between brackish and salt water?
September 6, 2010
As one of the folks who helped develop the ABYC’s Corrosion Certification for marine technicians and boat builders, I get a lot of calls from both boaters and technicians on what to do about marine corrosion issues. This call came in recently, and it is one that needs to be shared with all of our readers:
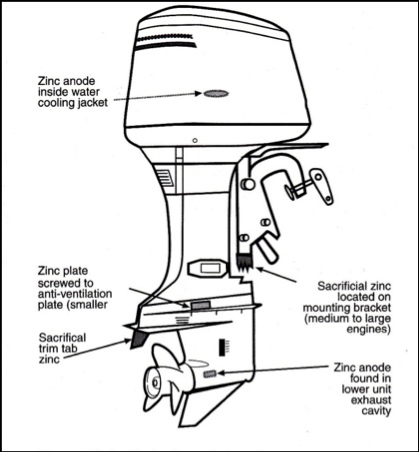
This diagram shows typical outboard engine anode zinc locations (from Outboard Engines, Maintenance, Troubleshooting and Repair)
Choosing the Right Anode
“My boat is in a marina that is located in brackish water. My mechanic says the anodes on my boat should be replaced with zinc since I often go fishing out in the Atlantic, which is of course salt water. I’ve heard this may not be the best thing to do. What’s the best choice for anode material for this situation?”
No Mystery Here
Of all the areas I deal in related to marine technology, the area that seems to be shrouded in the most mystery and intrigue is the matter of marine corrosion and cathodic protection. So, let me start by assuring all that there is no witchcraft or voodoo magic involved here. Contrary to popular belief (at least by some folks), it’s all science.
The answer in the above case is that, in fact, aluminum-alloyed anodes will be the best choice to provide cathodic protection for any boat that moves in and out of brackish or fresh water into salt water periodically.
There are three materials used for anodes in boating applications, aluminum, magnesium and zinc. The ABYC, in its cathodic protection standard called "E-2", provides a simple application table that looks like the one below.
The reason aluminum is the best choice here has to do with two factors. One, the relative conductivity of the water your boat is floating in. Two, the relative voltage potentials of the three different alloy metals used for anodes.

Three alloys are commonly used for cathodic protection; zinc should only be used in salt water, magnesium, only in fresh.
The issue here is that fresh and brackish waters are not as electrically conductive as salt water. With the three metals shown above, the inherent voltage potentials vary (all metals in electrolyte have a voltage potential). In this case magnesium has the highest potential, aluminum comes in next and zinc, last. Without getting into the esoteric explanation of the specific voltage potentials and potential differentials needed to achieve cathodic protection, understand this:
You need metal with a higher voltage potential to overcome the weak conductivity of the electrolyte (the water your boat is floating in). As you can see from the table, aluminum anodes provide the best compromise across the board. Zinc anodes may actually coat over (pacify) in brackish or fresh water and end up at a point where they will not function in any water chemistry.
By the way, it’s important to note that the magnesium anodes should only be used in fresh water. Their inherent voltage potential is too high for use in salt water and may actually cause over-protection of things like aluminum outdrives, sail drives and outboard engine lower units, causing extreme damage to aluminum castings.
Read more: All About Anodes
Advertisement
Advertisement